■ 圧力鋳込み成形の技法 ■
『圧力鋳込み成形』は、戦後復興の高度経済成長と共に、大量生産大量消費の時流に乗り開発された技術で、石膏型と機械を使う事でやきものの生地を大量に成形する事を可能にした、いわば機械化による成形技術と言えます。
(と言っても、完全オートメーションという訳ではなく、要所要所では人の手による作業も必要です)
それまでは、細工人など人の手により手間暇をかけて成形していた仕事を、石膏型と機械を使う事で、複雑な形状の器なども比較的簡単に、また、大量に成形することが可能になったため、
ロクロ成形や
型打ち成形で成形可能な製品でも
『圧力鋳込み』で成形されるケースが多くなった事もあり、肥前窯業界の、技術を必要とする
職人、ロクロ技術や型打ち技法の衰退、後継者不足を助長した一因とも言える面もあり、何でもかんでも
『圧力鋳込み成形』にしてしまう傾向には、ちょっと否定的な部分もありますが、それでも
『圧力鋳込み成形』で成形される製品の中にも、手作り感のある面白い形状の製品などを数多く同じような品質で作れる点など、
『圧力鋳込み成形』ならではの魅力的な作品も存在すると思います。
今回はその
『圧力鋳込み成形』の成形方法についてご紹介します。
⇒ こちらが
『圧力鋳込み成形』で
石膏型に陶土を注入する際の装置です。
縦に並んだ
石膏型は、複数の型を重ねたもので、ここでは1列に7個の
石膏型が重ねられていて、そのそれぞれの型は粘土が通る
穴で繋がるように作られています。
陶土はこの装置の下の台座に開けられた
穴から
石膏型の中に注入され、その際に
『高圧力』を掛けてすべての
石膏型に粘土を注入するため、
『圧力鋳込み成形』と呼ばれている訳です。
← こちらの
穴が、この装置の台座にある、
石膏型に陶土を注入するための
穴で、この
穴と
石膏型の
穴を合わせて複数の
石膏型を積み重ねます。
⇒ こちらは、陶土が注入された
石膏型を装置から取り外したところです。
石膏型は上下で外れるように作られており、
←こちらが型を外したところ。
画像奥、
石膏型の左側に粘土の柱が立っているのは、
石膏型の
穴を粘土が通った跡で、このようにして縦に積まれた
石膏型に、
穴を通して粘土が注入されている事が分かるかと思います。
⇒ 石膏型内側の作りを見ると、器の高台内側の部分に
小さな穴が開いているのが分かると思います。
(マウスオーバー画像で拡大出来ます)
手前にある大きな
穴が、粘土が
石膏型通るための
穴で、そこから横に移動して、器の高台内側の小さい
穴から器の型に粘土が注入され成形されます。
▲ 上画像の
石膏型を外した器の高台内側に小さな
粘土の突起が見えると思いますが、
この
突起が粘土の入り口の穴の跡であり、この
突起を取り除いた後に、この跡を目立たなくするための窯元の
←『刻印』などが押されます。
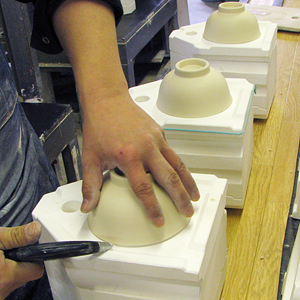
こうして成形された生地は、エアコンプレッサーを使って
石膏型から外され、ひとまず生地成形の完成のように思えますが。。。
実はまだ、生地の
乾燥と吹き上げの行程が残っています。
先にご紹介している
『排泥鋳込み成形の技法』の記事でも触れていますが、生地の乾燥作業も大変重要な作業となります。
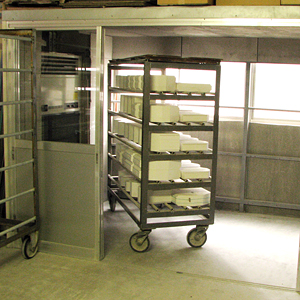
生地の乾燥については、一般的に自然乾燥に任せておられるところも多いと思いますが、この場合
『梅雨時』など季節によっても天候に左右される事が多くなるため、こちらの
『生地や』さんでは、生地と石膏型の乾燥用に
←『除湿乾燥室』まで用意されているほどです。
(生地だけでなく石膏型まで乾燥が必要なのは何故?と思う方もおられると思いますが、石膏型には吸水性があり、その特製で生地の水分を吸水して生地が型から離れやすくなるという利点があります。そのため成形作業前の石膏型も十分乾燥をさせておく必要があるためです。)
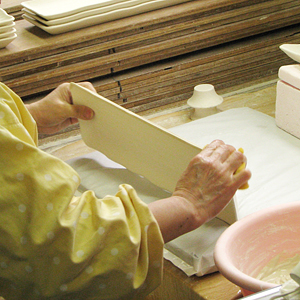
そして、十分乾燥させた生地の最後の仕上げは
『吹き上げ』の作業です。
⇒
水を含ませたスポンジで生地の表面や渕の部分を丁寧に吹き上げます。この作業は、鋭角な渕に丸みをつけたり、乾燥の際に生地の表面に浮き出て来る不純物などを取り除き、
焼成時の釉薬の乗りや仕上がりを良くするための作業で、この作業をおろそかにした場合、器の仕上がりの悪さにも繋がるため、生地をひとつでも無駄にしないための、地味でありながらも大変大事な作業となります。
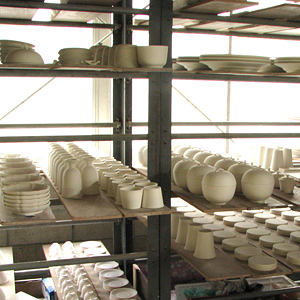
このようにして成形された生地は、有田周辺に点在する窯元さんの元に渡り、それぞれの窯元さんで
『素焼き焼成』『染付け絵付け』『本焼き焼成』『錦絵付け』『錦焼成』と、窯元独自のデザインで必要となる作業行程を経て、商品化されていきます。
★この
『圧力鋳込み成形』による成形の利点は、こちらの
『灰釉呉須線雲小鉢』⇒のようなちょっと
複雑な形状の器や、
↓『天竜青磁輪花牡丹彫皿』のように器の表面(表も裏も)に
彫りなどのデザインを施せる点が上げられます。
←こちらの製品は
『圧力鋳込み成形』で成形された製品ですが、それぞれの製品が
『圧力鋳込み』ならではの利点を活かして成形された製品だと思います。
このような製品に触れると、
『圧力鋳込み成形』には
『圧力鋳込み』なりの魅力がある事を再認識させられます。
<圧力鋳込み 一口メモ>
★ 見た目には他の成形方法との違いが分かり難い『圧力鋳込み成形』ですが、それを見分けるひとつの目安をここでご紹介します。上でも少し触れましたが、
皆さんは器の裏側を見て窯銘をチェックする時に、染付などで字で書かれている『窯銘』以外に『刻印』で押されている『窯銘』があって、その『窯銘』の入れ方の違いを疑問に思われた事は御座いませんか?
実はこの『刻印』こそが『圧力鋳込み成形』で成形された器を見分ける目安になるものです。このような『刻印』は、『圧力鋳込み成形』による『陶土』の注入口に出来る跡の上に、跡を目立たなくするために『刻印』を押す場合が多く、『刻印』が押された製品は『圧力鋳込み成形』で成形された製品である場合が多くなります。(作家さんなどによっては『刻印』を銘にされている方もいらっしゃいますので、すべての製品がこれに当たる訳ではありませんので、あくまでも目安と判断下さい)
また、『刻印』が無い場合でも注入口に出来る跡はどこかしらに残っていますので、そのような跡がある製品は『圧力鋳込み成形』で成形された製品だと分かります。窯銘をチェックする時には、ぜひ一緒にチェックしてみてください。
★ 『圧力鋳込み成形』の欠点のひとつに、成形を繰り返す度に石膏型の消耗で、器の生地が次第に厚くなって来てしまうという欠点があります。使用する型の消耗度によって、器の厚みに違いが出てくるため、比較的新しい型で成形した時には薄く上品に出来ていても、型が古くなってくると厚く重たくなるため、商品を追加する時などには厚さが違う製品になる場合があります。 (古くなって使用に堪えなくなった型については、新たに作り直されますので、作り直した直後の型で製作した製品は、また薄く上品に仕上がります)
★ 『圧力鋳込み成形』は、大量生産で作る製品についてコストダウンなどの点でメリットがありますが、少量生産の製品については逆にコストが掛かってしまう場合があります。『圧力鋳込み成形』で型を起こすか起こさないかの分岐点は、生産数量5000個以上がひとつの目安になっているようです。製品それぞれの特徴と、その製品の販売目的・プランなどに合わせて、どのような『成形方法』を選択するかも変わってくる訳ですね。
★ 関連記事
- 磁器成形方法の種類
- 型打ち成形の技法
- 排泥鋳込み成形の技法
- 細工の職人(機械ロクロ成形の技法)
- ゴッドハンド『ロクロの職人』(ロクロ成形の技法)